在新能源产业飞速发展的当下,锂电铜箔作为锂电池不可或缺的关键材料,其地位举足轻重。随着市场对锂电池性能的要求持续攀升,锂电铜箔的生产技术也在不断推陈出新。电磁感应加热辊作为一种新型加热设备,正逐渐崭露头角,在锂电铜箔生产过程中发挥着日益关键的作用,极大地提升了生产效率和产品质量,成为推动行业发展的重要力量。

得益于下游新能源汽车、储能以及 3C 数码等领域的持续强劲增长,电池需求呈现出爆发式增长态势,这无疑将带动锂电铜箔出货量稳步上升。据相关权威预测,到 2025 年,全球锂电池出货量有望达到 2227GWh,对应的锂电铜箔市场规模预计将突破 1076 亿元。与此同时,复合铜箔作为新型锂电池负极集流体材料,凭借其安全性高、成本低以及能量密度高等显著优势,随着技术的不断成熟和应用场景的日益拓展,市场渗透率也将不断提高。预计 2025 年,复合铜箔的市场空间可达 179 亿元左右,在乐观情况下甚至有望突破 291 亿元。
(二)技术进步极薄化趋势:为了提升企业自身的盈利空间并更好地满足客户端的需求,各大企业纷纷加快推进铜箔的极薄化进程。例如,GGII 预测,到 2025 年,厚度小于 6μm 的铜箔出货量市场占比将大幅提升至 50%。极薄化的铜箔不仅能够有效降低电池重量,还能提升电池的能量密度,满足市场对高性能锂电池的迫切需求。
复合铜箔技术改进:在未来,复合铜箔的生产工艺将持续优化,设备效率和良品率也将不断提升。这将有助于进一步降低生产成本,提高产品质量,从而推动复合铜箔在市场上得到更广泛的应用。通过技术创新,复合铜箔有望在锂电铜箔市场中占据更大的份额,成为行业发展的新亮点。
三、锂电铜箔生产工序锂电铜箔的生产一般需历经以下几个关键工序:
原材料准备:选用高纯度的铜作为生产原料,将其加热熔化形成铜液,这一步骤是后续成箔工序的重要基础。就如同烹饪美食需要优质的食材一样,铜的纯度和质量直接决定了铜箔的品质。高纯度的铜能够有效减少铜箔中的杂质,提高铜箔的导电性和稳定性,为生产高质量的锂电铜箔奠定坚实基础。
电解成箔:通过特定的电解工艺,让铜液在阴极上逐渐沉积,从而形成薄薄的铜箔雏形。这一过程犹如摊煎饼,需要精确的操作和严格的控制,才能确保铜箔厚度均匀一致。在电解成箔过程中,电流密度、电解液浓度以及温度等因素都会对铜箔的质量产生重要影响,因此需要严格把控每一个参数,以保证铜箔的质量稳定。
表面处理:对初步形成的铜箔进行表面处理,使其表面变得光滑、平整,达到所需的各项性能指标。这就好比给毛坯房进行装修,经过表面处理后的铜箔能够具备更好的使用性能。表面处理可以增强铜箔与电极材料之间的附着力,提高电池的充放电性能和循环寿命。
分切包装:将处理好的铜箔根据客户的具体需求进行分切,并进行妥善的包装,以便于存储和运输。分切过程需要保证尺寸精度,避免出现偏差,而包装则要确保铜箔在运输和存储过程中不受损伤。
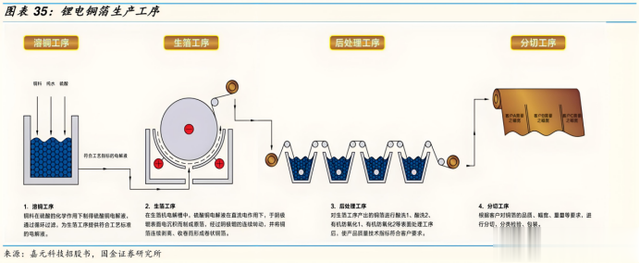
高效加热:电磁感应加热辊利用电磁感应原理,能够实现快速高效加热。高频电流通过励磁线圈产生交变磁场,导磁材料在交变磁场中会产生电涡流,电涡流促使金属原子相互碰撞产生热量。这种加热方式启动迅速,加热速度快,能够显著缩短生产周期,提高生产效率。与传统加热方式相比,电磁感应加热辊可以在短时间内将铜箔加热到所需温度,大大节省了生产时间,提高了企业的产能。
精准控温:电磁感应加热辊能够精确控制加热温度,温度调控精度极高,可实现拉伸温度与加热功率的闭环控制,确保铜箔在整个生产过程中始终处于适宜的温度环境。这有助于提高产品质量的稳定性,减少因温度波动而导致的质量问题。精准的温度控制可以保证铜箔在不同生产阶段的性能一致性,提高产品的良品率。
局部加热:该设备还可实现局部加热,例如在极耳区进行精准加热,同时减小对膜片区的影响,满足特定生产工艺的特殊需求。局部加热能够有效解决一些复杂工艺中的加热难题,为锂电铜箔的生产提供了更多的可能性。
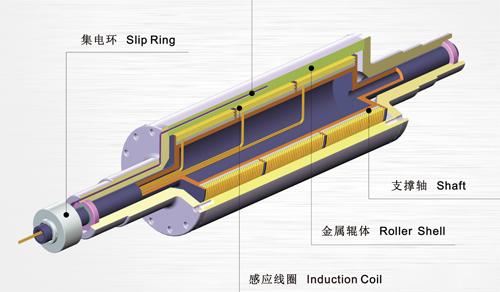
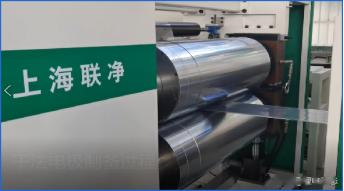
铝箔断带问题:在锂电池极片制造过程的辊压环节,采用常规的延展方式,很容易导致铝箔断带,这不仅会影响产品的良品率,还会降低产品的制程效率。电磁感应加热辊通过对极耳进行加热,使铝箔软化,在不破坏铝箔抗拉强度的前提下,增加铝箔的塑性,减少延展张力,从而有效降低断带率及断带频次。这一技术的应用,大大提高了锂电池极片的生产质量和效率,降低了生产成本。
温度均匀性问题:传统加热方式往往存在温度不均匀的弊端,容易导致铜箔质量不稳定。而电磁感应加热辊能够实现更均匀的加热,有效避免因干燥不均匀而引发的质量问题,显著提升产品质量。均匀的温度分布可以使铜箔在生产过程中受热均匀,避免出现局部过热或过冷的情况,从而提高铜箔的质量稳定性。
六、应用案例和效果分析某锂电铜箔生产企业在其生产线上引入了电磁感应加热辊。在引入之前,该企业深受铝箔断带率较高、产品质量不稳定等问题的困扰,导致生产效率低下,生产成本居高不下。引入电磁感应加热辊后,取得了显著的成效:
断带率显著降低:铝箔断带率从之前的 15% 大幅降低至 5% 以内,极大地提高了产品的制程效率,减少了因断带造成的材料浪费和生产延误。这不仅降低了生产成本,还提高了企业的生产效益。
产品质量提升:由于电磁感应加热辊能够实现精准控温和均匀加热,生产出的锂电铜箔厚度更加均匀,表面平整度和性能一致性都得到了显著提升,产品的良品率从原来的 80% 提升至 90% 以上。高质量的产品为企业赢得了更多的市场份额和客户信任。
生产效率提高:快速的加热速度使得生产周期大幅缩短,单位时间内的产量提高了 20%,有效提升了企业的生产能力和市场竞争力。企业能够在更短的时间内满足市场需求,提高了企业的经济效益和市场地位。
七、结论随着锂电铜箔行业的蓬勃发展,电磁感应加热辊凭借其高效加热、精准控温以及解决生产难点问题等诸多优势,在锂电铜箔生产中扮演着愈发重要的角色。通过实际应用案例可以清晰地看出,它能够切实有效地提升产品质量、降低生产成本、提高生产效率。在未来,随着技术的不断进步和创新,电磁感应加热辊有望在锂电铜箔生产领域得到更为广泛的应用,进一步推动锂电铜箔产业朝着更高质量、更高效益的方向发展,为新能源产业的蓬勃发展注入强大动力。
注:本站转载的文章大部分收集于互联网,文章版权归原作者及原出处所有。文中观点仅供分享交流,不代表本站立场以及对其内容负责,如涉及版权等问题,请您告知,我将及时处理。