一、涂布气泡对电芯性能的双重威胁
(一)显著降低电池核心性能
某锂电厂实测数据显示,当负极片气泡比例达到 40% 时,电池在 500 次循环后的容量保持率较无气泡电池下降 15% 以上,且放电平台明显衰减,说明气泡区域的锂离子嵌入 / 脱出效率显著降低,严重影响电池长期使用性能。
从微观角度来看,气泡在极片涂层中形成空洞,使得电子传导路径受阻。在充放电过程中,锂离子难以顺畅地在活性物质与电解液之间迁移 ,就好比道路上出现了许多坑洼,车辆(锂离子)通行变得困难,能耗增加,效率降低。
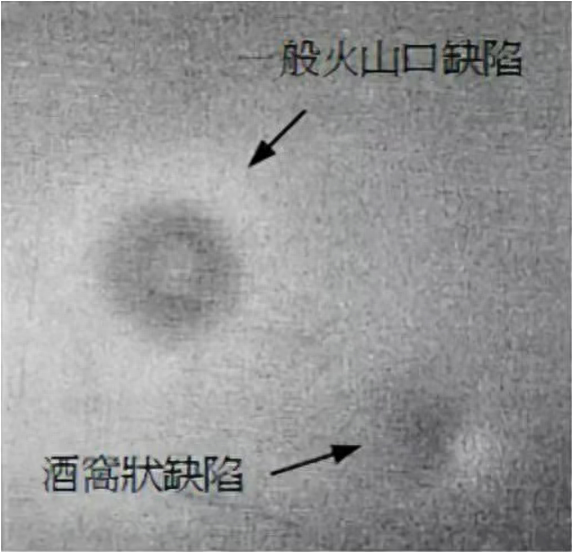
除了性能上的劣化,涂布气泡还为电芯埋下了安全隐患。气泡内部可能残留溶剂或空气,在电池充放电过程中,气泡区域因电阻异常易引发局部过热,长期循环可能导致负极析锂,形成枝晶刺穿隔膜,引发内部短路。某事故电池拆解发现,气泡密集区出现明显白色析锂层,周边碳层因锂离子嵌入不足呈暗灰色,验证了气泡是导致热失控和短路风险的重要诱因。
当电池快速充放电时,气泡处电阻产生的热量无法及时散发,就像一个不断升温的小热源。随着温度升高,负极材料中的锂开始以枝晶的形式析出,这些锂枝晶如同尖锐的针,不断生长,一旦刺穿隔膜,可能导致电池起火甚至爆炸。
二、涂布气泡的核心成因解析
(一)材料与浆料问题
异物污染
在锂电池生产的复杂流程中,一旦有粉尘、毛絮等杂质混入涂布液,就如同平静湖面投入石子,会激起层层 “涟漪”。这些异物会改变涂层表面张力,随着生产的进行,这些异物在涂层中 “捣乱”,烘干后在极片上留下了一个个圆形气泡痕迹。
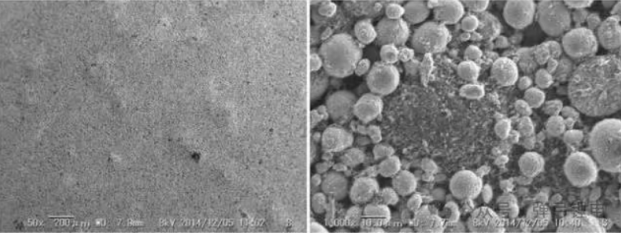
浆料混合缺陷
浆料混合是个精细活,搅拌不充分或未抽真空,空气就会混入其中,形成一个个微小的气泡 “隐患”。溶剂与粘结剂的润湿性也必须匹配,若两者 “不合拍”,就会像油和水难以相融一样,形成稳定的泡沫。曾经有一批次浆料,由于搅拌时间较正常缩短了 20 分钟,真空度也未达到标准要求,在涂布后,极片表面密密麻麻地出现了针孔状气泡,这些气泡虽小,但数量众多,导致该批次电芯容量一致性变差。
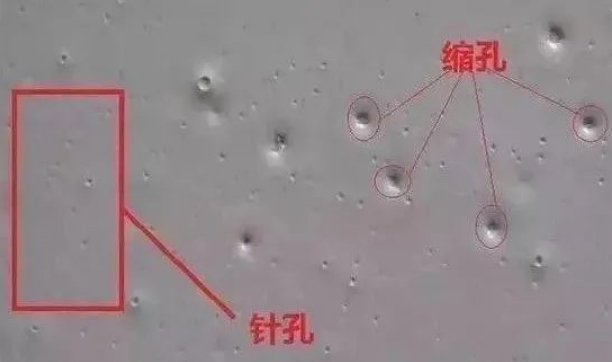
(二)工艺参数失控
涂布烘箱不当
干燥工艺是决定涂布质量的关键环节。烘干温度不足,溶剂就无法充分蒸发,如同潮湿的衣服未被彻底晒干,水分残留会在极片内形成气泡。风量不均同样是个 “大麻烦”,会使极片不同部位干燥程度不一致,导致局部溶剂残留。某厂在生产过程中发现,当干燥区温度维持在 80℃时,气泡率高达 5%。技术人员经过多次试验,将温度提升至 90℃后,溶剂蒸发更彻底,气泡率大幅降至 1.5%,这一数据有力地证明了溶剂蒸发不彻底是气泡产生的关键诱因。
涂布速度过快
当涂布速度过快时,就像快速画画难以保证线条的均匀流畅一样,浆料没有足够的时间流平。在高速涂布过程中,空气被快速裹挟进浆料中,却无法及时排出,这些空气就会在涂层中形成一个个气泡。某动力电池产线在提速过程中发现,当涂布速度超过 60m/min 时,气泡不良率显著上升,从原本的 3% 左右攀升至 8%,严重影响了产品质量,这表明涂布速度过快会打破浆料流平和空气排出的平衡,从而引发气泡问题。

(三)环境与设备因素
如果洁净度不足,尘埃粒子超标,就如同舞台上布满灰尘,会严重影响 “演出效果”。设备密封不良,如涂布机料槽未加盖,也会让外界杂质有可乘之机。某厂曾经因为生产环境洁净度不达标,尘埃粒子频繁落入,导致气泡报废率居高不下,一度达到 10%。后来,该厂投入资金升级洁净车间等级至万级,同时对设备进行密封改造,给涂布机料槽加上了严密的盖子。经过这些措施,气泡报废率大幅下降 60%,有效提升了产品质量和生产效益,这充分显示了环境与设备因素对气泡控制的重要性。
三、上海联净的技术突破路径
1. 干法工艺替代湿法
无溶剂工艺:直接采用干粉混合与热压成型,无需浆料调配、涂布和烘干,彻底消除溶剂挥发导致的气泡问题。
三维网络结构电极膜:通过高剪切混合使黏结剂(如改性PTFE)纤维化,形成三维交联结构,确保活性物质均匀分布,避免分层和团聚,提升电极密实度(达3.4g/cm³)。
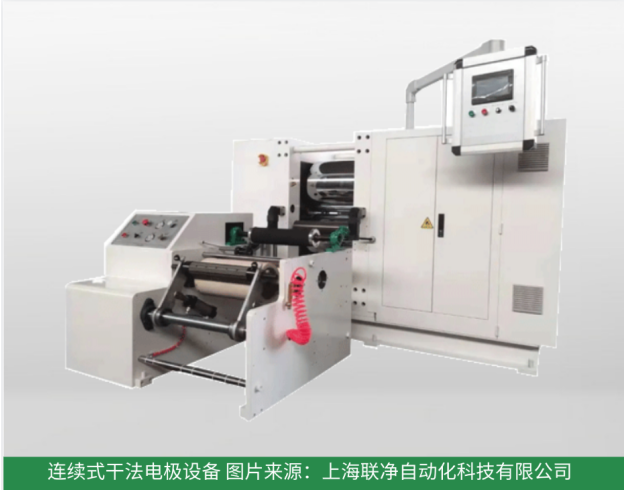
连续式干法电极设备 图片来源:上海联净自动化科技有限公司
2. 材料创新
复合黏结剂:开发PTFE与离子导电聚合物的复合黏结剂,增强电极机械强度,减少压制过程中的开裂风险,同时构建锂离子传输通道。
纳米添加剂:使用多级结构纳米材料防止粉体输送中的团聚、分层,确保电极膜均匀性。
3. 设备与工艺优化
高精度粉体输送系统:采用闭环动态控制技术,实现高黏性粉体的精确计量与输送,确保面密度均匀性(±1%)。
动态压延技术:引入高频振动和热辊多级压制,优化电极膜柔韧性与厚度一致性,避免传统湿法辊压中的应力集中问题。
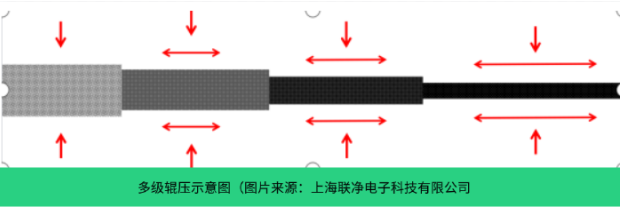
多级辊压示意图(图片来源:上海联净电子科技有限公司)
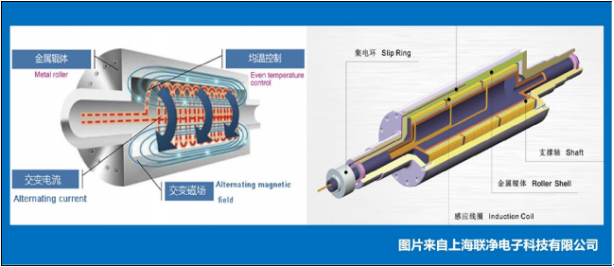
电磁感应加热辊(图片来源:上海联净电子科技有限公司)
4.实际效果与产业影响
消除气泡与提升良率:干法工艺使电极生产良率达95%,较传统湿法(约85%)显著提升,且无溶剂废气排放。
降低成本与能耗:省去溶剂回收环节,生产成本降低18%以上,能耗减少40%。
兼容高能量密度材料:可适配超高镍正极(如Ni90)和硅基负极,推动电池能量密度提升10%-20%。
5.对比传统湿法涂布气泡解决方案
传统湿法涂布需依赖真空脱泡、改进浆料配方等手段(如添加消泡剂、优化黏合剂分散性),而上海联净的干法技术从根源上规避了气泡问题,且具备更高的工艺稳定性和规模化潜力。
总结
上海联净通过干法电极技术革新,解决了锂电涂布中的气泡难题,同时推动行业向低成本、高性能、绿色化方向升级。其技术已进入中试验证阶段,并与头部电池厂商合作试产,有望重塑动力电池产业链格局。

文章来源:弹弓锂电、上海联净电子科技有限公司
注:本站转载的文章大部分收集于互联网,文章版权归原作者及原出处所有。文中观点仅供分享交流,不代表本站立场以及对其内容负责,如涉及版权等问题,请您告知,我将及时处理。